Executive summary
The semiconductor equipment manufacturing landscape has undergone a fundamental and rapid transformation over the last few years. Disruptions in the global supply chain and regulatory headwinds are also acting as catalysts in this transformation. As industry demand accelerates, mid-market semiconductor equipment manufacturers face both tremendous opportunity and existential challenges. The dual pressures of accelerated innovation cycles and stringent compliance requirements threaten to leave emerging and mid-market players behind as they compete with multinational giants possessing vastly superior resources. This thought leadership article examines how a fundamental shift in automation architecture, specifically through solutions like ICE Automate, is leveling the playing field, enabling emerging and mid-market manufacturers to thrive in an increasingly complex marketplace.
The new semiconductor reality – Speed as a strategic advantage
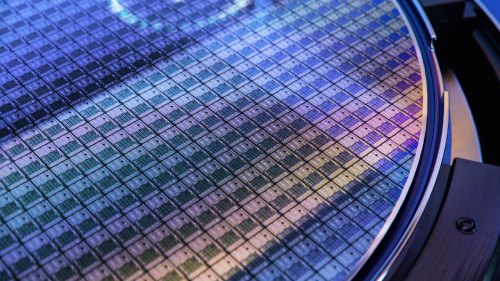
The semiconductor industry’s relentless drive toward advanced nodes has compressed development timelines to breaking point. Traditional equipment delivery cycles of 18-36 months are now fundamentally misaligned with the innovation velocity of chip designers racing to capitalize on AI and high-performance computing opportunities. This misalignment is particularly acute for mid-market equipment manufacturers.
The semiconductor equipment landscape has undergone a tectonic shift, establishing speed-to-market as perhaps the most critical strategic advantage. For emerging and mid-market manufacturers particularly, the ability to rapidly innovate and deliver solutions is no longer merely beneficial, it’s existential.
Why software can’t be an afterthought anymore
The semiconductor industry’s vulnerabilities became starkly apparent during the global pandemic. According to a 2024 Sourceability report, semiconductor shortages cost the global automotive industry alone more than $500 billion. Similarly, AlixPartners documented that semiconductor supply chain disruptions extended automotive production lead times by 20-52 weeks during the height of the chip shortage in 2021.
This disruption revealed something more structural than a temporary supply issue. The semiconductor equipment manufacturing model was built on assumptions of stability that no longer hold true. The industry’s traditional linear development approach, designing hardware first with software considerations secondary, creates inherent rigidity that hampers adaptability in today’s dynamic market.
Accelerating development cycles
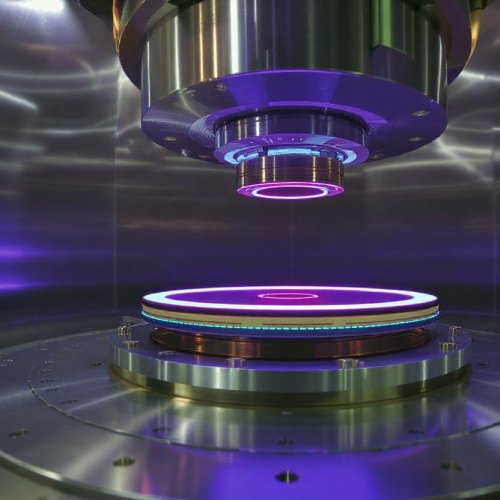
While the most visible supply chain issues had eased by the beginning of 2025, the lessons remain critically relevant. According to the KPMG Global Semiconductor Industry Outlook, 65% of semiconductor executives identified accelerating time-to-market as their highest strategic priority, ahead of both cost reduction and technical performance improvements.
This acceleration imperative is being driven by several converging factors:
- Technology acceleration: The pace of innovation in semiconductor manufacturing processes continues to increase, with new materials and architectures requiring rapid equipment adaptation
- Customer expectations: Chip manufacturers increasingly expect equipment providers to deliver solutions that align with their own accelerated roadmaps
- Competitive pressure: New market entrants, especially from Asia, are challenging established players with increasingly aggressive development timelines
- Capital efficiency: Faster development cycles mean more efficient use of R&D capital, a critical advantage for emerging manufacturers
- Equipment longevity: Chip demand forces fabs to extend equipment lifecycles, requiring decades-long reliable software.
For companies without the massive R&D budgets of industry leaders, this acceleration imperative presents both a challenge and an opportunity. Those who can adapt their development processes to this new reality can compete effectively despite resource limitations.
The cost of delay – Quantifying the financial impact
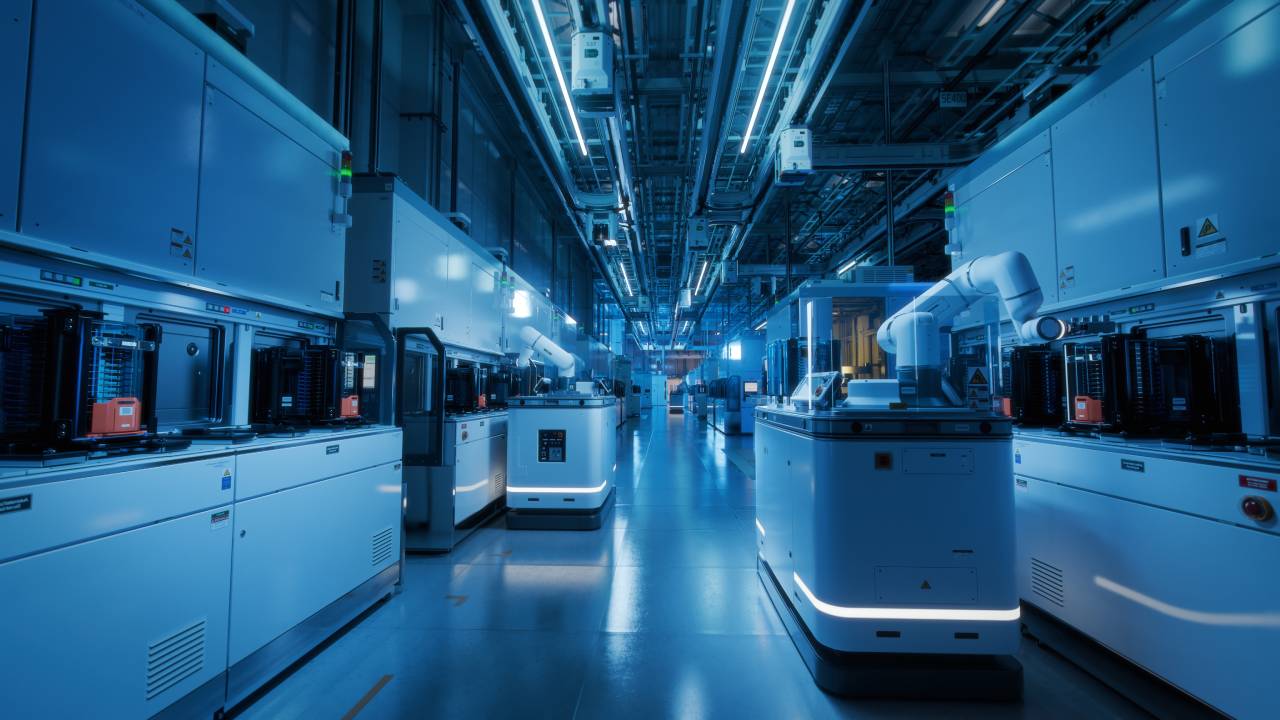
The financial implications of development speed are profound. According to a study by Boston Consulting Group on product development in capital equipment industries, companies that achieve top-quartile time-to-market performance generate, on average, 30% higher profit margins than competitors with average development timelines.
This impact is compounded by several factors:
- Premium price erosion: Early market entrants can command premium pricing while addressing unmet needs
- Opportunity cost: Resources tied up in extended development projects cannot be deployed to next-generation innovations
- Market window limitations: Semiconductor fabrication plants make equipment purchases during specific capacity expansion cycles; missing these windows can delay sales opportunities by months or years
Redefining time-to-market in the era of accelerated innovation

The time-to-market challenge manifests across multiple dimensions. For example, SEMI EDA Freeze 3 compliance now consumes software development resources, yet many tools still fail initial factory acceptance testing due to inconsistencies in implementation. This creates a vicious cycle: limited engineering resources are diverted to compliance and integration rather than genuine innovation.
ICE Automate’s architecture disrupts traditional development cycles through pre-validated compliance modules that compress factory acceptance testing from months to weeks. An optical inspection tool manufacturer from North America proved this transformation: their GEM implementation dropped from months to weeks after adopting ICE Connect (Host connectivity suite from Quest Global). Quest Global’s engineering support and ICE Host simulator enabled complete compliance verification before shipment, accelerating customer qualification dramatically.
For mid-market manufacturers, this compression of time-to-market represents more than incremental efficiency. It’s a fundamental competitive enabler. These faster development cycles allow emerging and mid-market companies to capture market opportunities that were previously inaccessible due to lengthy development timelines.
The software evolution in hardware-dominated environments
The semiconductor equipment industry has traditionally prioritized hardware excellence, with software often treated as an auxiliary component. This paradigm is now experiencing a fundamental shift, with software increasingly becoming the primary differentiator and value driver.
Beyond hardware – Software as key differentiator
According to SEMI’s Equipment Automation Technology report, software development now accounts for approximately 35-40% of total R&D spending for semiconductor equipment manufacturers, up from just 15-20% a decade ago. This trend reflects the growing importance of software capabilities in differentiating equipment offerings.
This transformation is being driven by several key factors:
- Hardware commoditization: Core hardware components are increasingly standardized, making unique hardware features harder to maintain as sustainable competitive advantages
- Higher throughput and efficiency: Robust software architectures and solutions improves equipment performance and overall efficiency.
- Data integration: Modern fabs demand equipment that smoothly connects with factory-wide information systems, requiring sophisticated software interfaces
- Value-added services: Predictive maintenance, remote diagnostics, and performance optimization, all software-dependent, are becoming critical value propositions
For mid-market manufacturers, this evolution offers a significant opportunity to compete against larger rivals. While hardware development demands substantial capital investment, software capabilities can be acquired more strategically through partnerships with specialized automation providers. This approach enables emerging and mid-market manufacturers to access enterprise-grade software capabilities without the overhead of building extensive internal development teams.
The user experience revolution
The influence of consumer technology has permanently altered expectations for industrial interfaces. According to the International Symposium on Semiconductor Manufacturing (ISSM) proceedings, fab operators reported 27% higher satisfaction and 19% fewer operational errors when using equipment with modern, intuitive user interfaces compared to traditional HMI designs.
This transformation extends beyond mere aesthetic appeal to fundamental operational advantages:
- Reduced training time: According to SEMI’s Workforce Development Survey, equipment with intuitive interfaces reduced operator training requirements by an average of 35%
- Error reduction: The International Electronics Manufacturing Initiative (iNEMI) documented that modern interface designs reduced setup errors by 24% in their Industry Benchmark Report
- Remote operation enablement: Advanced UI/UX design facilitates effective remote monitoring and operation, increasingly important in distributed manufacturing environments
Solving the R&D cost puzzle
The financial dynamics of automation represent perhaps the most significant barrier for mid-market equipment manufacturers. Traditional automation platforms impose a double financial burden: substantial upfront capital expenditure followed by ongoing compliance maintenance costs that divert precious R&D resources away from differentiation. When combined with implementation services, the five-year total cost of ownership becomes an untenable financial burden that directly impacts emerging and mid-market manufacturers’ ability to fund innovation.
ICE Automate’s per-equipment licensing model fundamentally realigns these economics, converting what was once a capital-intensive investment into an operational expense that scales with success. This approach liberates R&D budgets from compliance overhead, enabling emerging and mid-market manufacturers to focus investment on genuine differentiation rather than table-stakes functionality.
The financial impact creates real market advantages. A North American etch equipment manufacturer with limited resources used ICE Automate to reach market within 6 months, securing repeat orders and driving substantial revenue growth. This demonstrates how the right software partnership transforms financial constraints into competitive speed for specialized manufacturers.
Build vs. buy – A strategic turning point
For semiconductor equipment manufacturers, particularly those in the mid-market category, the decision between developing software platforms internally and licensing established solutions represents a critical strategic choice with far-reaching implications.
Uncovering the long-term costs of internal development
The full cost of internal software development extends far beyond initial programming expenses. According to the Standish Group’s CHAOS report, only 31% of software development projects were delivered on time, on budget, and with the required features. In complex technical environments like semiconductor manufacturing, this success rate drops to just 16.2%.
The cost structure includes:
- Initial development: Beyond programmer salaries, this encompasses requirements analysis, architecture design, project management, and quality assurance resources
- Specialized expertise acquisition: According to SEMI’s Workforce Survey, semiconductor automation specialists command salaries 23% higher than comparable software engineers in other industries, reflecting their scarcity
- Ongoing maintenance: The IEEE Software Engineering Institute estimates that maintenance typically consumes 60-70% of total software lifecycle costs, with teams spending more time maintaining existing code than developing new capabilities
- Knowledge dependency risk: Custom systems often create critical dependencies on specific individuals who understand system intricacies, creating business continuity risks
The CapEx to OpEx transition
The financial structure of software acquisition can significantly impact both balance sheet composition and investor perceptions. According to PwC’s Technology Forecast, 72% of industrial technology companies are actively shifting from capital-intensive in-house development to per-equipment licensing technology acquisition models.
The semiconductor equipment sector has begun recognizing these advantages. Automation platforms like ICE Automate have pioneered financial models that convert what would traditionally be a multi-million dollar capital expenditure into a more manageable operational expense structure, aligning with investor preferences for capital efficiency and controlled R&D spending.
The road to zero downtime manufacturing
For semiconductor equipment manufacturers, product quality has a critical metric: unscheduled downtime. In advanced semiconductor manufacturing, where each hour of tool downtime represents significant costs in lost production, equipment reliability has evolved from a competitive advantage to a fundamental requirement.
Traditional approaches to equipment reliability focus on reactive maintenance and basic statistical process control. While effective to a degree, these approaches fall short in addressing the complexity of modern semiconductor processing, where subtle interdependencies between components can trigger cascading failures that evade conventional monitoring.
ICE Automate’s modular architecture was developed by veterans with deep software and semiconductor expertise. It ensures reliability, maintainability, and configurability. A deposition equipment manufacturer from South Korea adopted ICE Automate more than 15 years ago, and those tools still run with record low MTBF and virtually no unscheduled downtime.
Compliance as a competitive advantage
In the highly regulated semiconductor manufacturing environment, standards compliance has evolved from a necessary burden to a potential source of competitive differentiation.
The SEMI standards landscape – Navigating complex industry requirements
The semiconductor equipment industry operates within an extensive framework of standards. According to SEMI’s official standards catalog, the organization maintains over 1,000 active standards documents across 24 technical domains, with dozens of revisions published annually.
Key standards affecting semiconductor equipment manufacturers include:
- Communication protocols: Standards like SECS/GEM, EDA/Interface A, govern how equipment communicates with factory systems
- Software architecture: Emerging TOGAF standards address software modularity, configuration management, and security
Making compliance automatic by design
The compliance burden for semiconductor equipment manufacturers has grown exponentially with each successive generation of SEMI standards. For example, the latest EDA Freeze 3 standards mandate requirements that disproportionately burden emerging and mid-market manufacturers with limited compliance engineering resources.
Traditional compliance approaches require months for implementation and validation of updated standards. This timeline creates a critical competitive disadvantage for emerging and mid-market manufacturers who must either divert engineering resources from innovation or delay market introduction while larger competitors move forward.
ICE Automate transforms compliance from burden to advantage through pre-validated libraries that implement latest SEMI standards out of the box. The built-in SEMI standard compliance validator automatically identifies potential compliance issues during development rather than during customer factory acceptance testing.
A recent case study from a sub-20nm metrology tool deployment illustrates this transformation. During Samsung’s 2024 audit cycle, the manufacturer reduced compliance-related tool downtime significantly compared to competitors. This reduction directly translated to improved customer confidence and accelerated qualification timelines.
Standards compliance and factory integration
The time between equipment delivery and productive operation represents a critical performance metric. According to the SEMI Equipment Integration Capability Benchmark Study, complete standards compliance reduced average production qualification time by 38%, from 5.7 weeks to 3.5 weeks.
Leading automation platforms have demonstrated the ability to further reduce factory acceptance time through built-in compliance with SEMI standards, accelerating revenue recognition and customer satisfaction while reducing integration costs.
Standards enable global expansion
Geographic market expansion presents significant growth opportunities and introduces complex regulatory and integration challenges. The International Trade Administration’s Semiconductor Manufacturing Equipment Market Intelligence report indicates that equipment requiring significant customization for regional requirements typically experiences market entry delays of 4-9 months compared to solutions with global standards compliance.
For emerging and mid-market manufacturers with limited global infrastructure, this simplified market access can be transformative, enabling geographic expansion with minimal additional resource investment.
The user experience revolution
While semiconductor manufacturing has always prioritized function over form, a significant shift is underway in customer expectations regarding equipment interfaces. As experienced operators retire and a new generation enters the workforce, familiar expectations from consumer technology are reshaping requirements for factory equipment. “Today’s operators expect their equipment to be as intuitive as their smartphones,” notes industry experts. “When your interface looks like it was designed in 1995, you’re fighting an uphill recruitment and training battle.”
Quest Global, as a technology and design powerhouse, ensures ICE Automate uses the latest technologies across the stack based on fab requirements. We select best-of-breed tools and implement the architecture in compliance with semiconductor manufacturing industry standards.
A Japan-based clean tool manufacturer implementing these interface enhancements reported higher operator productivity and faster operator training cycles. For emerging and mid-market equipment manufacturers competing for customer mindshare against larger rivals, this level of interface sophistication represents a critical differentiation point that directly impacts purchase decisions.
Engineering support ecosystem
In the semiconductor equipment market, the product itself is only one part of the customer value. Extending equipment lifetime depends on engineering services for maintenance, sustenance, and refurbishing. A solid support ecosystem drives competitive success.
Responsive support as a competitive edge
According to VLSI Research’s Customer Satisfaction Survey for Semiconductor Equipment, “technical support and responsiveness” ranked as the second-most important selection criterion, with 67% of respondents rating it as “extremely important” in purchasing decisions, behind only equipment performance.
For emerging and mid-market manufacturers, responsive engineering support offers a particularly powerful differentiation opportunity, as organizational agility can often outpace larger competitors with more complex approval and implementation processes. Access to extensive engineering resources, such as those provided by global engineering firms like Quest Global with its 20,000-strong global engineering team, can provide the responsive customization capabilities that market leaders demand.
The support infrastructure advantage for global reach
As semiconductor manufacturing becomes increasingly distributed across global regions, the ability to provide responsive, culturally attuned support has evolved from luxury to necessity. This requirement presents particular challenges for mid-market equipment manufacturers lacking vast global service organizations.
ICE Automate supports language switching so operators can work in their preferred language. It also adapts layouts and workflows to regional norms, improving operator efficiency and satisfaction.
A German optical inspection equipment manufacturer with deployments in Europe and Asia resolved most support requests within hours, outperforming industry SLA benchmarks. For emerging and mid-market manufacturers competing with large multinational service organizations, this capability turns support from a weakness into a competitive advantage.
The next innovation horizon – Preparing for tomorrow
Looking forward, semiconductor equipment manufacturers face challenges that go far beyond today’s technical specs. As the industry embraces Industry 4.0, advanced packaging, and heterogeneous integration, tomorrow’s innovation will be shaped by architectural choices made today.
Beyond the push for AI-enhanced process control and the growing pressure of SEMI EDA compliance, a new paradigm is taking hold in control system design: EtherCAT-based architectures. Industry leaders like Lam Research and Applied Materials have already standardized EtherCAT for their next-generation tools, setting the pace for automation at scale. For mid-market manufacturers, adopting this architecture could be key to staying competitive, bringing deterministic performance, real-time synchronization, and cost-effective scalability into the core of equipment design.
AI/ML Integration – Transforming equipment functionality
Artificial intelligence and machine learning technologies are rapidly transforming semiconductor equipment from passive tools to active partners in manufacturing optimization.
According to a study published in IEEE Transactions on Semiconductor Manufacturing, fabs implementing AI-enhanced equipment control systems reported average yield improvements of 5.3% and throughput increases of 11.7% compared to traditional rule-based control systems.
These technologies are creating value across multiple functional domains:
- Predictive maintenance: Identifying potential failures before they occur by recognizing subtle pattern changes in equipment performance
- Process optimization: Continuously refining process parameters to maximize yield and throughput
- Anomaly detection: Identifying unusual patterns that may indicate quality issues or optimization opportunities
ICE Automate’s roadmap includes frameworks for data analytics and AI/ML integration. This will let equipment manufacturers leverage these technologies without building in-house data analytics and AI development expertise.
Collaborative development – Accelerating innovation through ecosystems
The increasing complexity of semiconductor manufacturing has made isolated innovation progressively more difficult. Equipment providers who establish effective collaborative ecosystems gain a significant advantage in innovation velocity. Research published in the International Journal of Production Economics found that semiconductor equipment manufacturers engaged in structured collaborative development released new product generations 27% faster than those relying primarily on internal development resources.
For emerging and mid-market manufacturers, collaborative models are particularly valuable as they provide access to innovation resources that would be impossible to maintain internally, effectively leveling the playing field with larger competitors.
ROI calculation – Measuring the full financial impact
A thorough return on investment analysis provides essential justification for transformation investments. The most compelling analyses include:
- Time-to-market value: Quantifying the revenue impact of shorter development cycles
- Capital efficiency improvement: Calculating the financial advantage of shifting from CapEx to OpEx models
- Quality impact: Assessing the financial benefit of improved product quality and reduced defect density.
The new economics of equipment innovation
The semiconductor industry stands at an inflection point where traditional approaches to equipment development, particularly for mid-market manufacturers, are becoming fundamentally unsustainable. The challenges of compressed timelines, financial constraints, reliability expectations, compliance requirements, and support demands require not incremental improvement but architectural reinvention.
ICE Automate’s approach represents precisely this reinvention, transforming automation from cost center to strategic enabler through three fundamental shifts:
First, pre-validated compliance modules compress tool development cycles significantly, enabling emerging and mid-market manufacturers to capitalize on market opportunities previously inaccessible due to time constraints.
Second, per-equipment licensing model economics convert capital traps into manageable operational expenses, preserving precious R&D funds for genuine differentiation rather than table-stakes functionality.
Third, Quest Global’s global locations and engineering services team provide integration and customization of ICE Automate, develop digital solutions, and deliver bespoke software—all at cost-effective rates through our India operations.
The 4-6x time-to-market acceleration advantage
The most compelling transformation metric lies in development process modernization. Case studies show semiconductor equipment manufacturers implementing modern automation platforms have reduced software development cycles from typical 24-36 months to just 3-6 months.
This 4-6x acceleration represents genuine competitive disruption. Emerging and mid-market manufacturers can now outpace industry giants in bringing innovation to market. Companies adopting ICE Automate’s integrated approach have achieved previously impossible market introduction timelines.
In today’s semiconductor equipment landscape, speed-to-market defines competitive advantage. Mid-market manufacturers that adopt modern development approaches can turn their biggest vulnerability into a differentiator. As SEMI standards evolve and digital solutions reshape fab operations, platforms like ICE Automate help these manufacturers stay at the innovation frontier.